Project Background
The founder of this 3D printer company worked as an engineer at GE, Motorola and Makerbot. He was one of the first people in the world who was able to retail a 3D Printer for less than $1,000. The first four generations of the 3D printer were made in New York, until he decided to make the fifth generation in China to save on cost.
This 3D printer is designed for use in the consumer's home. No manual calibration is required, just take it out of the box and it is ready to print.
The item includes parts below:
Plastic parts:
· 27 pcs Metal parts
· External 180w power supply
· 5 pcs Standard components
· 15 pcs PCBs
· 75 pcs
· 110 pcs Screw
· Creates plastic parts up to 8" x 8" x 8“
· Resolution up to 1mm
· 15" x 15.4" x 19.2" footprint (L x W x H)
· On/Off Power Switch
· Weight - 18 lbs
· SoliTouch Technology
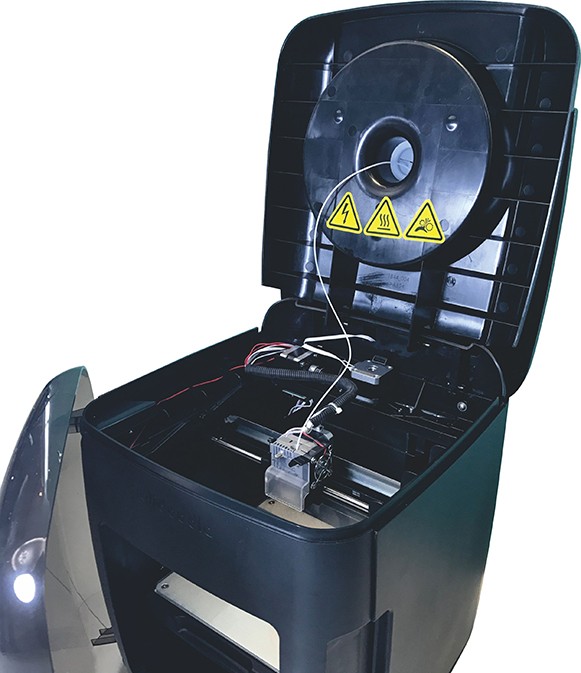